Blog-News
Ian Hancock is Presenting “Air Classification From Industrial Processing To Specialized Applications” at the Powder & Bulk Solids Conference
Powder & Bulk Solids Conference Tech Talk: Air Classification From Industrial Processing to Specialized Applications
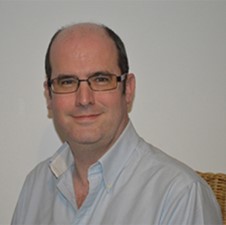
Ian Hancock, Eng Tech MIET IEng FIMechE; Vice President, Sales & Operations – Bradley Pulverizer
Presented by Ian Hancock, Eng Tech MIET IEng FIMechE; Vice President, Sales & Operations – Bradley Pulverizer
Wednesday, April 26th at 1:30 in the Tech Theater
Air classification is a common processing technique employed for the separation of coarse products from fines. While traditionally used in the minerals industry for heavy-duty applications, the need for classification of specialized powdered materials and for hygienic applications is growing. This session will chronical the evolution of the Bradley Pulverizer Windsifter Air Classifier from its historic roots in industrial mineral processing to the newly designed stainless steel classifier, ideal for highly specialized applications. Topics presented will include:
Operational Considerations for Optimal SSP Manufacturing in the Broadfield Process
Part 5 of a 5-part blog series: “The Bradley Broadfield superphosphate process”
The Broadfield process has remained a mainstay of the global phosphate industry since its introduction in the 1930s. In Part 1, Ian Hancock, Vice President Sales & Operations, Bradley Pulverizer, provides an introduction to the Bradley Superphosphate process, in Part 2 we explore the origins of superphosphate manufacturing , Part 3 outlines the chemical process for SSP manufacture, and Part 4 explains the overall system and processes. Click Here to download the complete article in pdf format as published by BCInsight Ltd in Fertilizer International Sept|Oct 2022, issue 510, pp. 31-35.
Acidulation in the Broadfield Den is a continuous process that requires good coordination between the various feed streams and equipment so they operate together in equilibrium. However, as ideal process conditions are almost never met in practice, Bradley’s Broadfield Dens and Belt Dens are designed to operate effectively at between 60-110 percent of their rated output. This provides operators with the necessary flexibility to adjust for changes in feed composition and/or plant conditions while ensuring that consistent end-product quality is maintained. Some of the key operational considerations are highlighted below.
Rock blend. Individual phosphate rock sources and shipments will have different parameters for total phosphorus content, reactivity rates, impurity levels (i.e., cadmium), fluorine volatilization, and odorous compounds. To adjust for these differences, rocks from different sources are blended to establish the desired chemical composition and achieve the necessary ‘operational window’. This is important as the chemistry of the rock blend will directly influence the equilibrium of the entire system, including milling fineness, acid concentrations, mixer speeds, den residence time, and granulation conditions etc.
A Spotlight on Joe Tittermary: Presenting at NSSGA’s Pulverized Minerals Division (PMD) Annual Meeting – March 15, 2023
Joe Tittermary, Technical Business Development Manager at Bradley Pulverizer will be speaking at NSSGA’s Pulverized Minerals Division (PMD) Annual meeting at the 2023 NRMCA, NSSGA & PCA Joint Annual Convention on March 15th. He will be discussing options available for efficiently meeting demanding particle size specifications for both new milling and air classification systems as well as plant retrofits. Additionally, he will focus on the capability to simultaneously produce multiple streams/cuts of products with differing particle size specifications.
A Spotlight on Nikheel Mistry: Presenting “Reducing Emissions in the Size Reduction and Drying Industry” at IMechE Seminar – 07 March 2023
Nikheel Mistry, Project & Process Commissioning Manager at Bradley Pulverizer, will be speaking at IMechE’s Bulk Handling for Net-Zero conference on March 7, 2023. His presentation “Reducing Emissions in the Size Reduction & Drying Industry” will cover three primary topics:
- Efficient milling techniques
- Efficient drying techniques
- Optimized plant design for reduced emissions
Overview:
Now, more than ever, the UK bulk materials industry is pushing to operate in a more efficient and environmentally friendly way. Companies need to be more sustainable in their approaches and consider how to decarbonize processes, whilst reducing risk, cost and emissions. There is also a need to look at waste reduction across bulk materials handling processes and how we can create a circular economy within the UK to support net-zero.
Superphosphate Acidulation in the Broadfield Den
Part 4 of a 5-part blog series: “The Bradley Broadfield superphosphate process”
The Broadfield process has remained a mainstay of the global phosphate industry since its introduction in the 1930s. In Part 1, Ian Hancock, Vice President Sales & Operations, Bradley Pulverizer, provides an introduction to the Bradley Superphosphate process, in Part 2 we explore the origins of superphosphate manufacturing , and Part 3 outlines the chemical process for SSP manufacture. Click Here to download the complete article in pdf format as published by BCInsight Ltd in Fertilizer International Sept|Oct 2022, issue 510, pp. 31-35.
The Broadfield Den is a turnkey system specifically designed to continuously acidulate inert phosphate rock into water soluble superphosphate (Figure 1). In detail, it is actually comprised of a series of individual and interlocking equipment systems. Ultimately, proper calibration and maintenance of this entire system is required to ensure continuous production and profitable operation.
The information provided in this article assumes ‘typical working conditions’ based on general operational experience. In practice, however, each Broadfield Den is individually engineered for optimal output. Units are designed to meet the conditions specified by the end user, as well as the results of laboratory trials and testing, with confirmation of raw material composition being of primary importance.
Superphosphate production begins with the grinding of insoluble phosphate rock (mainly fluorapatite, Ca3(PO4)2CaF2) to a fine powder. This upstream process is carried out by a milling system, such as the Bradley BM20 Airswept Roller Mill, to generate phosphate rock particles of specified fineness (Figure 2). Typically, for sedimentary rock, the specified size is 75-90 percent passing 75µm (200 Tyler mesh), whereas igneous rock, due to its lower reactivity, is typically ground finer to 90+ percent passing 53µm.
Making Single Superphosphate (SSP) and Triple Superphosphate (TSP) in Broadfield Process Units
Part 3 of a 5-part blog series: “The Bradley Broadfield superphosphate process”
The Broadfield process has remained a mainstay of the global phosphate industry since its introduction in the 1930s. In Part 1, Ian Hancock, Vice President Sales & Operations, Bradley Pulverizer, provides an introduction to the Bradley Superphosphate process, and in Part 2 we explore the origins of superphosphate manufacturing . Click Here to download the complete article in pdf format as published by BCInsight Ltd in Fertilizer International Sept|Oct 2022, issue 510, pp. 31-35.
Single Superphosphate (SSP) is made by reacting non-soluble fluorapatite (the mineral present within phosphate rock) with sulphuric acid to produce soluble monocalcium phosphate and calcium sulphate. Gaseous by-products from the reaction include and (released from associated calcium carbonate in the rock). The overall chemical reaction is summarized in equation 1 below.
2Ca5(PO4)3F+6H2SO4+3H2O → 6CaSO4+3Ca(H2PO4)2∙H2O+CaF2
Enhancing Efficiency of Ultra-Fine Air-Classification of Powders to Facilitate Global Reductions in Carbon Emissions from Food and Transport
Throughout Bradley Pulverizer’s history, we have collaborated with leading research institutions on particle milling and air classifying research initiatives and presentations.
Recently, the prestigious Wolfson Centre at the University of Greenwich partnered with us on a very exciting project involving the use of the Bradley Stainless Steel Windsifter Air Classifier. This project is significant for its focus on standalone air classification equipment, an often under-appreciated factor for meeting stringent specifications and increasing yields. This research provides scientific data to support important advancements in air classifier design. The study focuses on improving efficiencies of ultra-fine powder classification across protein shifting plant-based proteins to produce meat substitute. Improving the sharpness of cut of fine particle powders and high value materials can play a role in meeting stringent specifications and yield requirements across a variety of industries.
Zaki Hussaini, MEng, Design Engineer at Bradley Pulverizer, is a PhD candidate and researcher on this project.
The following is reproduced from the University of Greenwich, Wolfson Centre for Bulk Solids Handling Technology.
Origins of Superphosphate Manufacturing
Part 2 of a 5-part blog series: “The Bradley Broadfield superphosphate process”
The Broadfield process has remained a mainstay of the global phosphate industry since its introduction in the 1930s. Ian Hancock, Vice President Sales & Operations, Bradley Pulverizer, explains its continuing success in superphosphate production worldwide. Click Here to download the complete article in pdf format as published by BCInsight Ltd in Fertilizer International Sept|Oct 2022, issue 510, pp. 31-35.
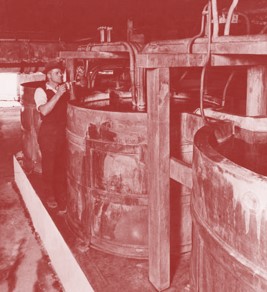
The early days of Acidulation
It is well known that crops require a supply of nitrogen, phosphorus and potassium for their sustenance – and that using fertilizers to correctly control the soil’s NPK balance is therefore essential for the long-term sustainability and commercial viability of agriculture.
While phosphorus is abundant in nature, the majority is locked away in insoluble form within crystalline phosphate rock. Indeed, phosphorus in its natural form offers little nutritional benefit to plants, as these can only absorb nutrients from the soil solution. That means there is a need to convert insoluble phosphate rock into plant-available soluble phosphates to support the productivity of global agriculture.
Introduction to the Bradley Broadfield Superphosphate Process
Part 1 of a 5-part blog series: “The Bradley Broadfield superphosphate process”
The Broadfield process has remained a mainstay of the global phosphate industry since its introduction in the 1930s. Ian Hancock, Vice President Sales & Operations, Bradley Pulverizer, explains its continuing success in superphosphate production worldwide. Click Here to download the complete article in pdf format as published by BCInsight Ltd in Fertilizer International Sept|Oct 2022, issue 510, pp. 31-35.
The Bradley Broadfield process is the global standard for single super phosphate (SSP) manufacturing. Its flexible and reliable design is based on more than 100 years of SSP manufacturing experience and can produce SSP economically from all known phosphate rock sources.
The process is also used to make:
- Triple superphosphate (TSP)
- Monoammonium phosphate (MAP)
- Diammonium phosphate (DAP)
- Monocalcium phosphate (MCP)Dicalcium phosphate (DCP)
- Partially acidulated phosphate
- Synthetic gypsum
- Iron sulphate
- Other acidic salts
A Comparison of Mills Used for Phosphate Rock Grinding
There are similarities and differences between the mills that are most commonly used for commercial phosphate grinding. The following insight into the performance variables across the mill types helps to determine which mill is the right fit for specific phosphate grinding applications.
A brief introduction of 3 common mill types:
- Ball Mills – a horizontal rotating cylinder containing a charge of steel balls. The balls tumble as the mill turns and material caught between the balls is ground to powder.
- Table-Roller Mills – a horizontal table rotates with spring-loaded rollers mounted above. Material fed into the center of the table passes underneath the rollers and is ground to powder.
- Pendulum-Roller Mills – vertical rollers rotate inside a fixed horizontal ring. Material fed between the rollers and ring is ground to powder.
Similarities across the mills:
All 3 mill types require a continuous controlled feed, regulated to keep optimum conditions. This is done by selecting a suitable variable to control – noise is the standard method for ball mills; motor amps or pressure drop are used for roller mills. Also, all phosphate mills operate as air swept systems, using air to remove fine particles from the grinding zone to reduce the cushioning effect that they exert. This allows the grinding action to be concentrated on the large oversize particles, and is the key to efficient milling.